Faster cutting. Lower costs. Faster deliveries. 3 and 5-axis hydro-abrasive cutting is an absolutely innovative technology in Italy.
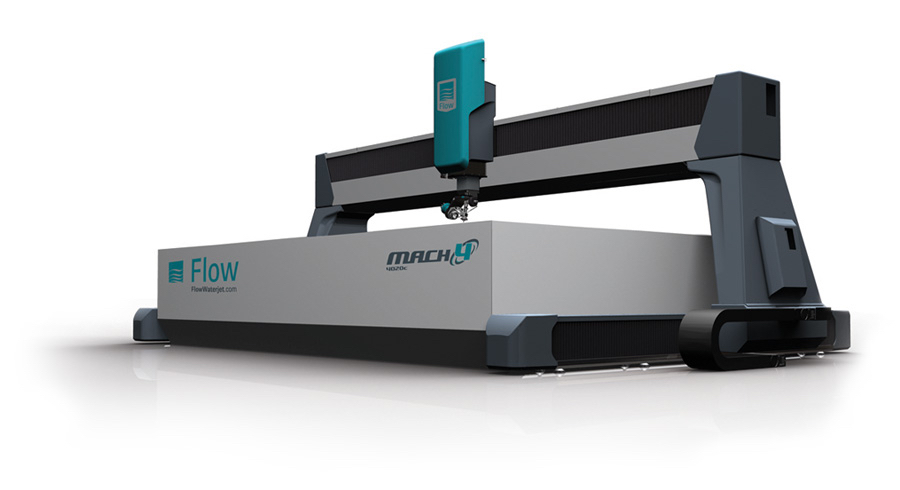
We are immensely proud to have some of the top machines using this technology, such as the Mach 4 by Flow, (inventor of waterjet cutting and one of the world’s leading manufacturers) which can cut with a pressure of up to 6500 bar, the maximum pressure reached for waterjet cutting.
There are 2 unwanted inherent effects that all waterjets have when they cut through the material: jet taper and stream lag. Here are a few aspects to help point out the difference between a traditional waterjet cutter and a top quality waterjet cutter.
TAPER
This is the lateral deviation that the jet undergoes while it cuts through the material and has a taper effect, which is also called "elephant paw."
STREAM LAG
During processing, the cutting head advances along the designed path and the trajectory of the jet is slightly curved and not straight as it passes through the material: the exit point of the stream at the bottom of the material trails behind the entrance point of the stream at the top of the material (the side the stream enters).
The coarser the cutting finishes, the faster the cutting head advances, which accentuates the arched trajectory of the jet; its exit point from the lower face will always be further back than its entrance point.
The distance between these 2 points is the stream lag, the effects of which are more evident in direction changes, especially if "internal" right angles or very acute angles need to be cut.
When the cutting head changes direction, an uncontrolled stream tail (due to this lag) negatively erodes the workpiece, generating non-conforming parts.
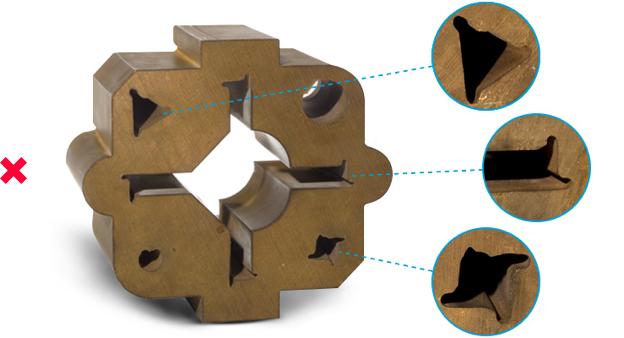
Incorrect exit profiles without Dynamic Waterjet
Correct exit profiles with Dynamic Waterjet
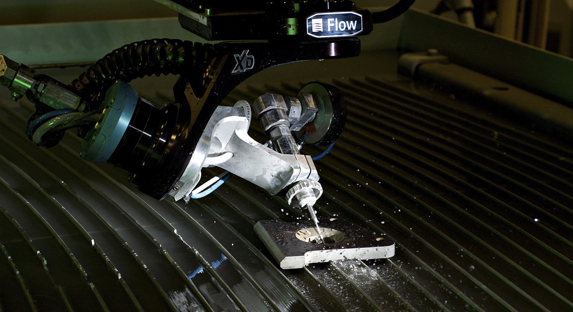
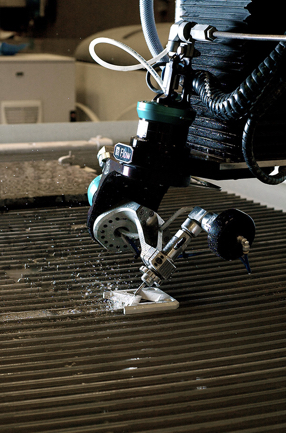
Comparative cutting
Waterjet | Plasma | Laser | EDM | |
---|---|---|---|---|
Secondary processing |
Generally none. Waterjet is a cold cutting process that leaves a perfectly smooth edge. |
Typically yes. |
Sometimes. |
Generally none. Very shallow HAZ. |
Materials |
Any material |
Mainly steel, stainless steel and aluminium |
Mainly steel, stainless steel and aluminium. It can also cut a variety of other materials |
Only conductive materials |
Thickness |
Almost any material up to 60 cm. The Z-axis constraint is the only thickness limit. |
Up to 5-7.5 cm, depending on the material |
Generally 2.5 cm or less, depending on the material |
Generally 30 cm or less |
Precision |
Fino a 0,025 mm |
Up to 0,25 mm |
Up to 0,025 mm |
Up to 0,0025 mmm |
Edge comparison | ![]() |
![]() |
![]() |
![]() |
Perfectly smooth edges are immediately obtained with the waterjet system. Secondary processing is often required with the other cutting technologies in order to obtain the same perfectly smooth edge produced by the waterjet.